Myco-Block
Myco-Block is an airy, dimensional material that can be used to build solid volumes and forms. It can be cut, drilled, joined, partially sanded, and painted on.
-
Lightweight, Insulating
-
Saw Dust and Mycelium, Water
-
Band Saw, Table Saw, Drilling, Adhesives
Myco-Materials
Myco-Sheet
Myco-Sheet is a novel formulation: a thin, rigid and dense (similar to MDF) material that functions structurally well and can be used as operatable flat components.
-
Durable, Strong
-
Coffee Grounds, Mycelium, Water
-
Laser Cutting, Drilling, Sanding, Band Saw, Table Saw, Drilling, Adhesives
Myco-Paste
Myco-Paste is an extrudable mycelium paste that can be used in additive manufacturing applications. This process is under development and will be ready by 2025.
-
Versatile, Extrudable, Live
-
Saw Dust, Mycelium Culture, and Wheat Bran.
-
Sculpting, Molding, 3D Bioprinting
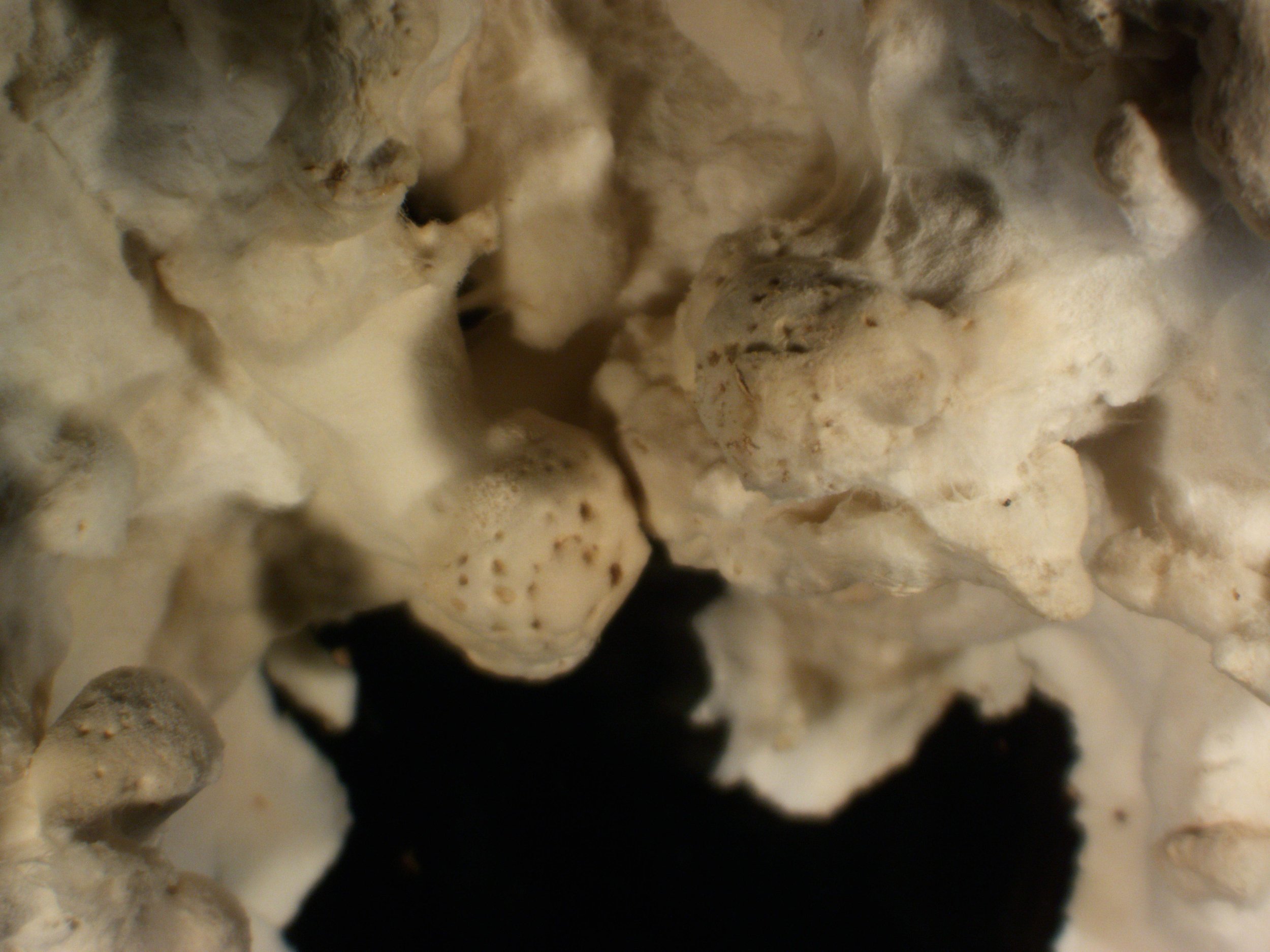
Capturing 200 grams of C0₂ on average per block.
Myco-materials are carbon-negative, capturing more waste and carbon than they produce at a local microsystem, being biodegradable at their end of life.
They are safe to use, customizable and highly versatile.
Material Qualities and Characteristics
Mechanical Properties
-
177 to 542 g/cm^3
-
0.17 to 0.46 MPa for custom samples loaded in a universal testing machine.
-
130-190% in 24 hours when fully submerged in water.
-
Observed under a scanning electron microscope for hyphal density and connectivity for insights on insulation.
Experiential Attributes
-
Attributes such as curiosity and comfort are common for both myco-materials. Myco-sheets felt relatively familiar and had a more neutral response.
-
Myco-sheets invoke calmness and a sense of nature, being a bit rough on the edges. Myco-sheets are more elegant, strange and sexy, feeling natural yet manufactured. They both feel futuristic.
-
Myco-blocks feel warm, elastic and lightweight with a matte texture. Myco-sheets are colder and feel strong yet lightweight with a smooth texture.
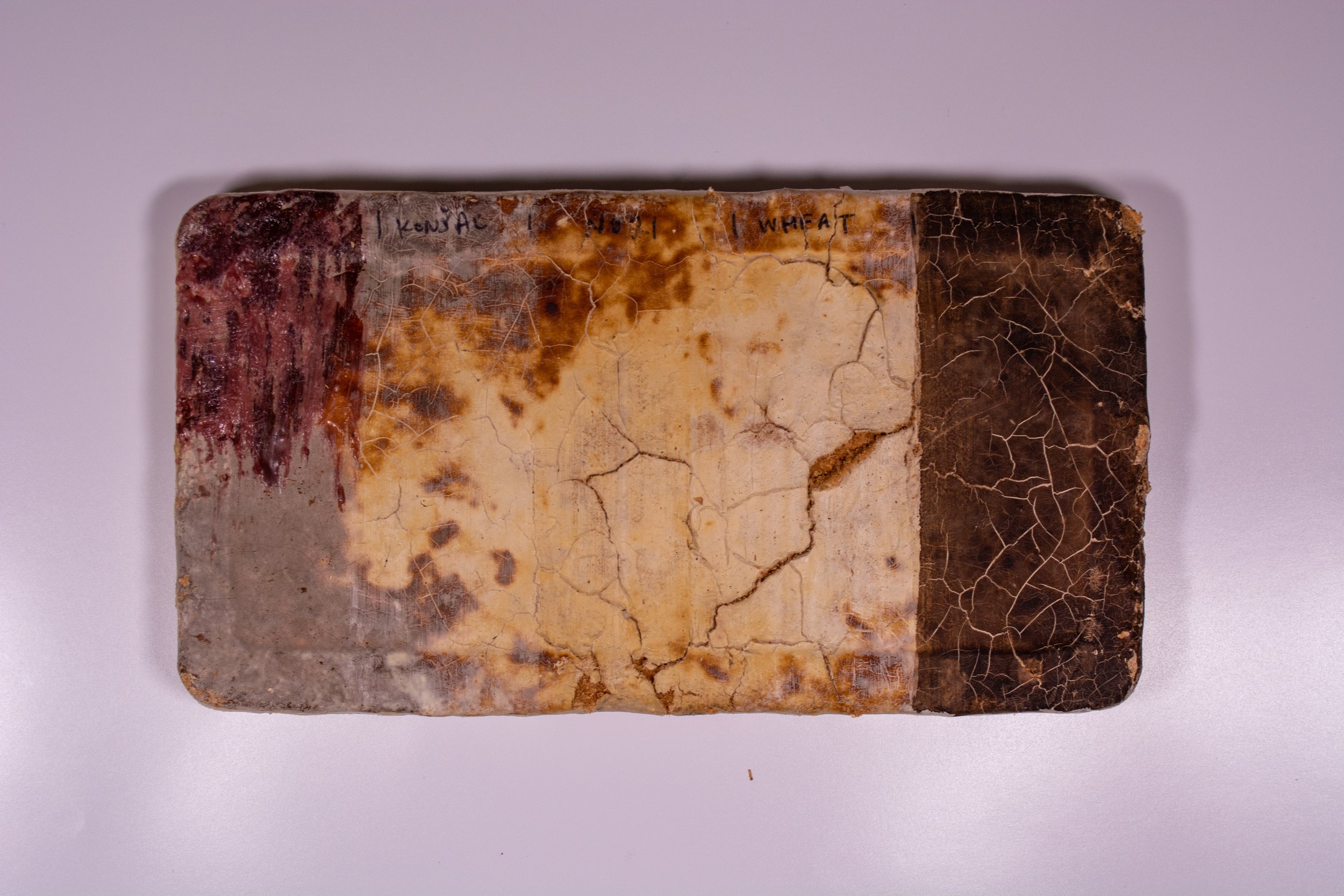
Bio-based and Non-Toxic Surface Enhancements
In collaboration with local papermaker and RISD faculty Haley MacKeil, we tested surface treatments typically applied in handmade paper on our Myco-Block material.
-
Red beeswax created a water-resistant coating on the Myco-Block and tinted the surface color.
-
A plant starch often used in Japanese paper making to create strength. Applied to the surface of the Myco-Block, it brought out the natural colors of the material and formed a smooth, crackled finish.
-
The nori finish behaved similarly to the Konjac, but with a slightly more transparent, yellow-tinted finish.
-
Wheat starch mixed with water caused deep cracks in the surface while doing little to impact appearance.
-
Locally-sourced walnut dye coated the Myco-Block in a nearly opaque layer of deep brown and a crackle finish.
-
Water-based coatings that can be applied in thin layers and dry quickly can create interesting surface effects, though do not provide the same benefits as when they are incorporated into paper. Oil or wax-based coatings function similarly as they do on paper, binding with the surface to create a flexible, water-resistant layer.
A Simplified Growth Process
-
1. Feedstock & Strain Sourcing
Mycelium can feed on a number of organic waste products. We chose local waste streams that were plentiful in Providence, RI and at RISD—coffee grounds from cafés and sawdust from woodshops.
-
2. Mold Preparation & Sterilization
In order to create optimum growing conditions for the mycelium and reduce the possibility of materials becoming contaminated with other microorganisms, all work surfaces, tools, containers, and hands must be sterilized before beginning.
-
3. Mycelium Inoculation
Mycelium from a selected medium (grow-kits, spores, spawn or liquid culture) is mixed into the feedstock using a mold to hold the shape, and is covered with a thin film to maintain moisture and avoid contamination.
-
4. Growth Phases
With optimal humidity, ventilation and temperature, mycelium grows through the feedstock and on the outer surface of to bind it into a solid structure, over the course of several days to a couple weeks.
-
5. Dehydration and Extraction
The grown mycelium material can be removed from its mold and dehydrated in a oven, heat-press or sun-dried to end the mycelium life. The material can then be post-processed and is ready for use.
-
FAQs
-
Our pre-fabricated mycelium materials are dehydrated, sterile and safe-to-use. Mycelium materials are alive during the growth process and die when they are dehydrated under heat in the last stage of our process. Live mycelium objects are possible too, and need to be handled with care and attention to keep them that way.
-
Mycelium materials are biodegradable under soil in 6-8 weeks. In water, they take longer to break down, closer to 12 weeks. We can also compost mycelium waste at the end of the product life cycle.
-
Mycelium materials are unique and have an experimental making process. By growing mycelium with custom compositions and conditions, we can also tune specific properties. Currently it is difficult to work with processes such as wire-cutting and CNCing due to its internal structures.